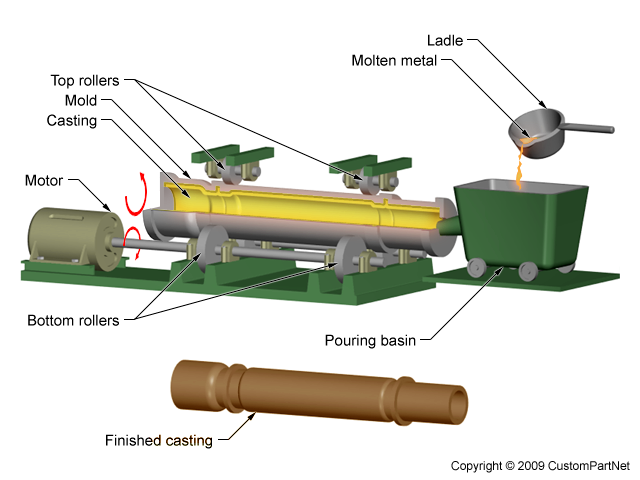
CENTRIFUGAL CASTING PROCESS
-
CENTRIFUGAL CASTING PROCESS
– A family of casting processes in which the mold is rotated at high speed so centrifugal force distributes molten metal to outer regions of die cavity this process known as Centrifugal Casting Process. This process is widely use for the Pipe manufacturing.
Types of Centrifugal Castings
- True Centrifugal Casting
- Semi-Centrifugal Casting
- Centrifuge Casting
-
True Centrifugal Casting
- Molten metal is poured into a rotating mold to produce a tubular part
- In some operations, mold rotation commences after pouring rather than before
- Rotational axes can be either horizontal or vertical
- Parts: pipes, tubes, bushings, and rings
- Outside shape of casting can be round, octagonal, hexagonal, etc , but inside shape is (theoretically) perfectly round, due to radially symmetric forces
-
Semi Centrifugal Casting
- Centrifugal force is used to produce solid castings rather than tubular parts
- Molds are designed with risers at center to supply feed metal
- Density of metal in final casting is greater in outer sections than at center of rotation
- Axes of parts and rotational axis does not match exactly Often used on parts in which center of casting is machined away, thus eliminating the portion where quality is lowest Examples: wheels and pulleys G factor keeps from 10-15
-
Centrifuge Casting
- Mold is designed with part cavities located away from axis of rotation, so that molten metal poured into mold is distributed to these cavities by centrifugal force
- Used for small parts
- Radial symmetry of part is not required as in other centrifugal casting methods